Metal Injection Molding vs Investment Casting
Metal injection molding vs Investment casting are both cost-effective manufacturing technologies for high-quality metal components. Therefore, it is difficult to choose the most suitable metal manufacturing process: MIM or investment casting. All these decisions will affect the final cost-per-part, then ultimately affect the bottom-line profits.
Metal Injection Molding
Metal injection molding (MIM) is a unique hybrid technology in metal manufacturing. It combines the process of plastic injection molding and powder metallurgy, finally create net-shape metal components.
MIM process starts from the feedstock compounding, super-fine metal powders (< 22μm in average) are mixed with binder materials, which is consisting of a primary paraffin wax materials and a secondary thermoplastic polymer. Then extrude and chop the resulting mixture into tiny pellets as MIM feedstock.
A normal injection molding machine will heat and inject MIM feedstock into a mold cavity under high pressure. In order to create high volume molded parts (green parts) with required geometry. These green parts will be debinded and sintered into a net-shape metal component with tight tolerance. In addition, secondary process is available to increase surface finish or other properties.
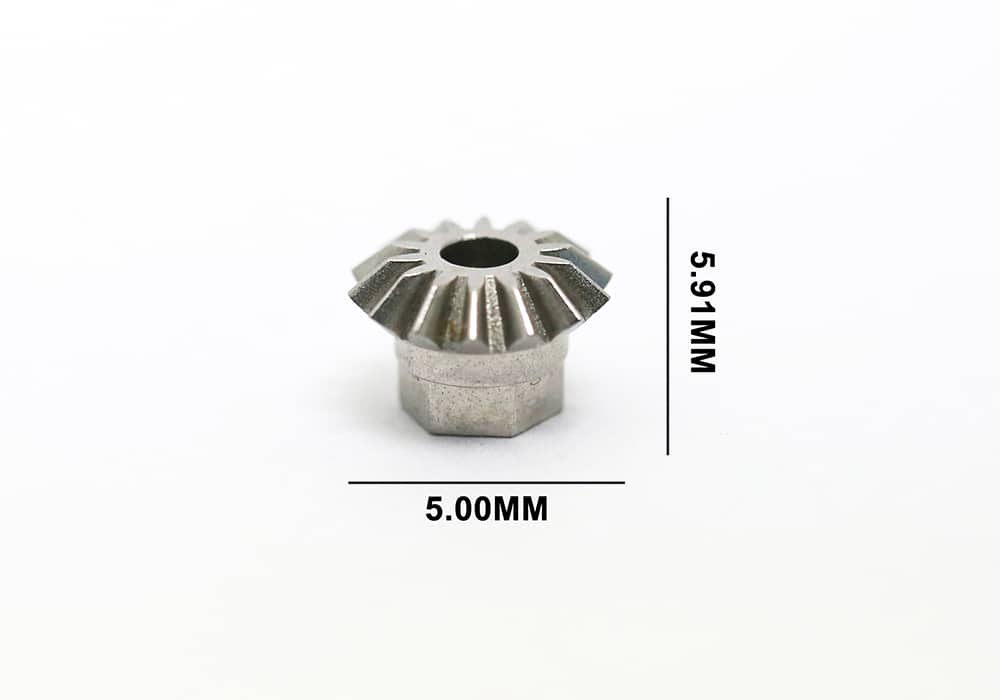
Investment Casting
Investment casting is also known as lost-wax casting, it is one of the diverse casting methods in metal parts manufacturing. Comparing to other casting technologies (sand casting or die casting), investment casting provides high dimensional accuracy, smooth surface finish, design complexity and fast production.
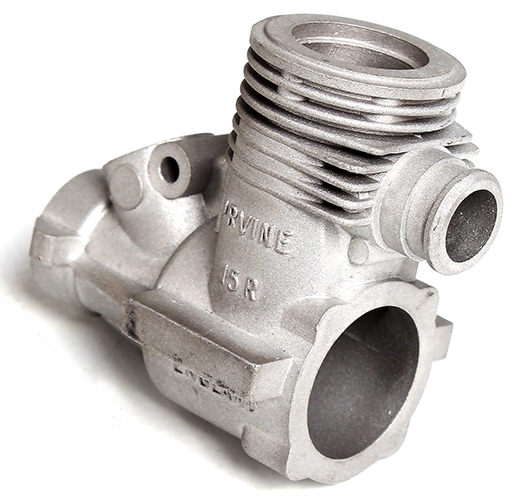
Investment Casting Process
IC (investment casting) apply wax-like materials to create expendable patterns, then manufacture complex metal parts with high precision. In addition, ceramic molds with elite thermal quality result in incredible surface finish. The main manufacturing process:
Creating Master Pattern
The master pattern is the replica of final metal parts with the same details, there is also an allowance for thermal contraction or shrinkage. This mater pattern is reusable for numerous casting cycles as a standard. Common material for mater pattern dies are wax, wood, metal, and silicone rubber. Different material choice depends on various factors like pattern life, design complexity, thermal expansion or contraction, surface quality. Operators will apply the master pattern to produce wax patterns for every casting cycle.
Conventionally, wax patterns are made from die casting. Nowadays, new technologies like 3D printing is popular in pattern manufacturing, in reason of its decent accuracy and low cost.
Wax Pattern Assembly
All wax patterns should be assembled into a single investment casting mold, this combined pattern is known as ‘tree’. Operators will assemble the patterns with a sprue/runner/riser network, this gating network provides the pathway for liquid metal, in order to flow smoothly into all parts of the mold.
This assembly process is manual or robotic. For low volume production, or each casting with different design, it is optimal for manual assembly. Otherwise, for repetitive casting, it is wise to apply robotic assembly units.
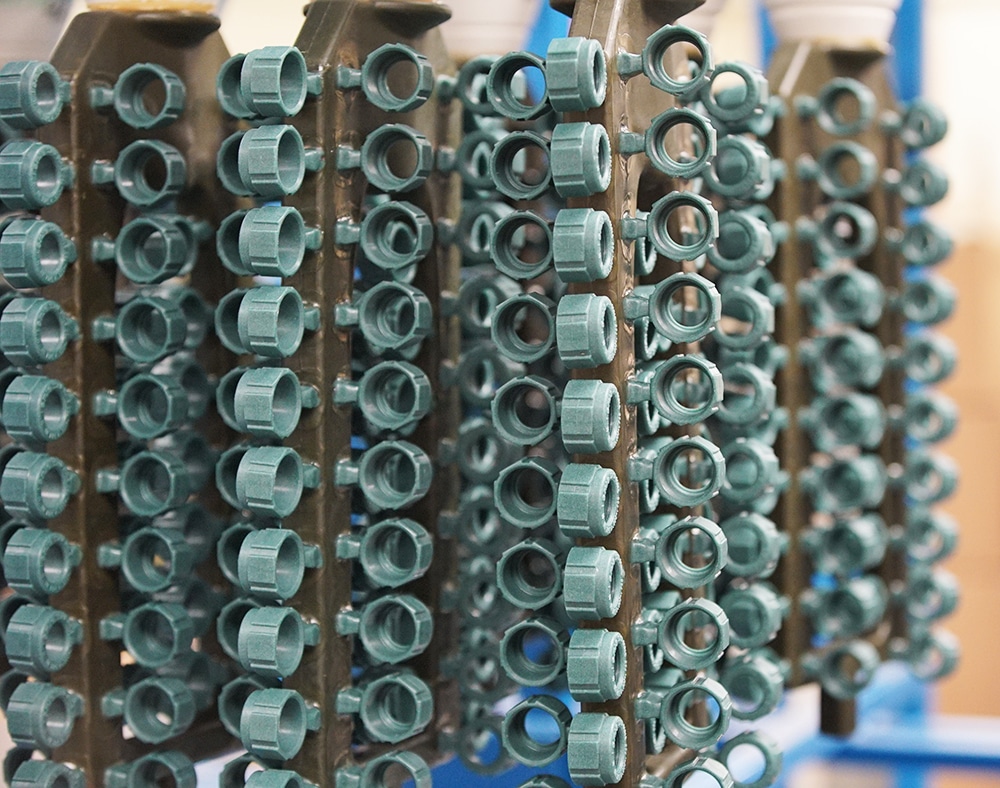
Creating Mold Shell (Dipping)
Operators apply a coat of refractory materials onto the wax pattern, this coating process is in multiple dipping cycles. The ‘tree’ is dipped repeatedly into a bath of ceramic slurry and sand stucco with gradual and rotary motion. The ceramic will increase the temperature-resistance of mold, and stucco will enhance its strength.
In each dipping cycle, the thickness of ceramic shell is increasing. It is critical to apply the initial layer (primary core), as it has significant effect on quality and geometry of the final parts. The dipping process is repeated until achieve the required shell thickness. Depending on the casting size, weight and materials, the typical shell thickness range from 9.5 mm to 13.0 mm. For heavy metal parts or high melting temperature metal, we should increase the shell thickness to bear the temperature and stress.
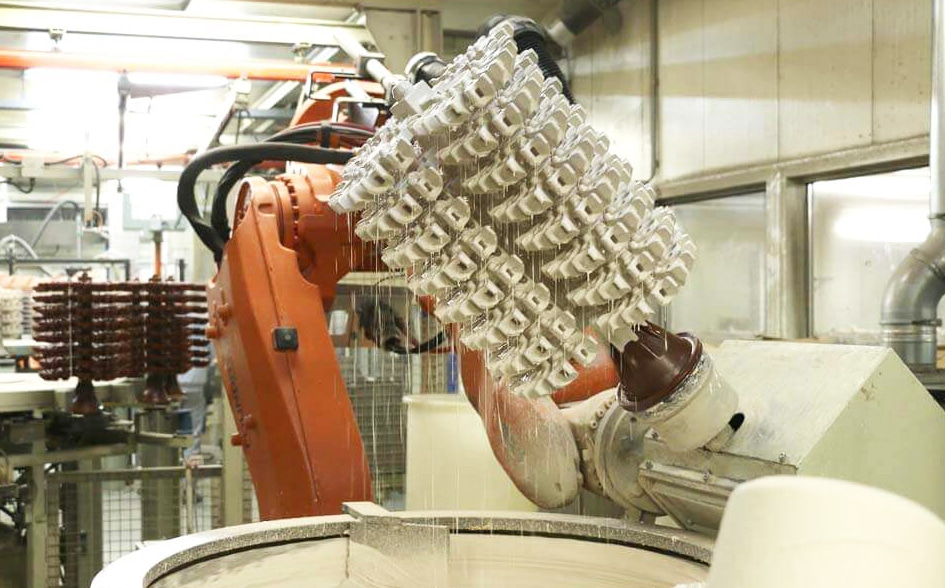
De-waxing
The wax is removed from the ceramic shell by melting, normally, we apply autoclaves to fire furnaces to heat and melt the wax. The mold will be place upside down, so molten wax will flow out easily. In autoclave, the majority of wax will flow out at 90℃-175℃temperature for 12 hours. Then bake the mold at high temperature of 1000℃for a few hours, in order to burn off the remaining was and evaporate moisture content.
Dewaxing is a crucial stage in the whole casting process, such intense temperature will give rise to many potential defects in the mold shell, such as cracking. In this process, heat treatment also has some positive effect on refractory materials. It improves the strength of shell, and decrease its reactivity with molten metal.
Preheating & Casting
The mold is preheated at a specific temperature, in order to minimize its thermal shock once in contact with high-temperature liquid metal. Then liquid metal will be poured into the mold in a controlling manner. The pouring rate is critical to minimize turbulence-related casting defects. In addition, it is suggested to create a vacuum environment once molten metal tends to react with air. After the pouring process, the molten metal will cool down and solidify inside the mold, then create the metal casting.
Nearly any alloy can be manufactured by this casting process. Air melting or vacuum melting are dictated by the alloy chemical properties. Vacuum melting is utilized for alloys with reactive elements in air.
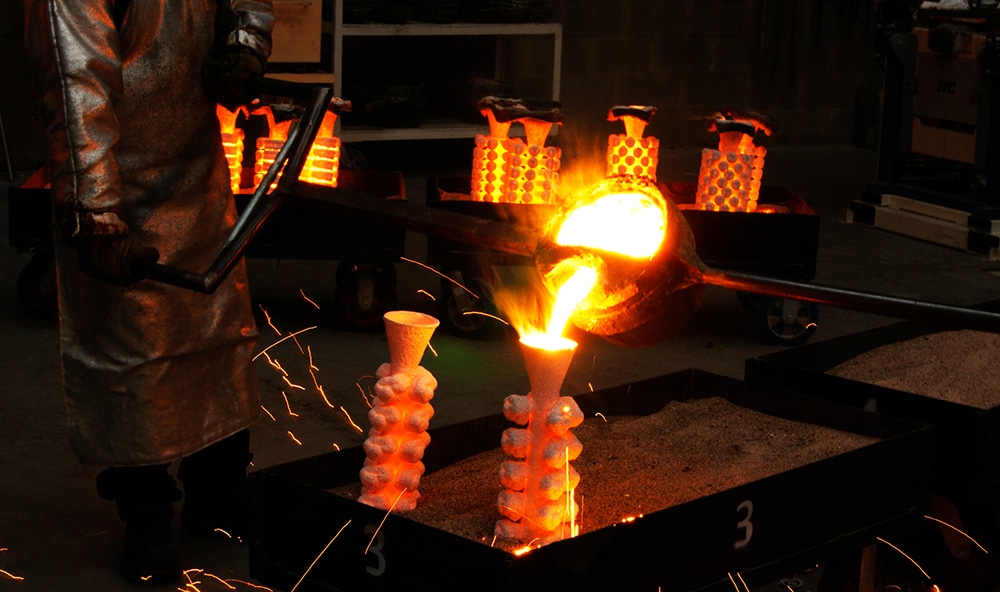
Post-processing
The mold shell will be broken down in a knockout operation, once the casting metal cools and solidifies sufficiently. These ceramic molds are knockoff by hammer or water jetting. After that, the casting parts will go through several semi-finishing operations, in order to achieve required dimensions and properties.
Firstly, the gates and runners (gating system) are cut off. Meanwhile, grinding or blasting technology are able to flat rough surfaces, jagged edges, and other defects. Moreover, machining like milling and drilling can finish holes and surfaces. In addition, other surface finish treatments can be applied to achieve high surface quality.
Investment Casting Advantages
Investment casting technology has numerous advantages, this makes it an informed decision for metal manufacturing.
- Compatible complex geometry: Investment casting can create intricate geometries, including internal features, sharp curvatures, thin walls, and shallow passages. All these features can be manufactured in one single part, without additional joining operations via welding.
- Fine surface finish: The surface finish of investment casting can reach to 3 microns(μm), this is better than sand casting. Moreover, investment casting parts have no parting lines, this enhances part aesthetics.
- Wide part size: This technology can produce different part sizes, from lightweight as 100g to heavy as 1 ton. These wide part sizes have the same quality, no matter huge turbine blades or minute medical equipment.
- High dimensional accuracy: This technology is a net-shape casting process with minimal finishing tolerances. After additional finish treatments, the impressive dimension tolerance can reach to ± 0.075 mm.
- Various Material Selection: It is compatible with numerous metal materials. It can produce steels, nickel alloys, aluminum alloys with the same quality and precision.
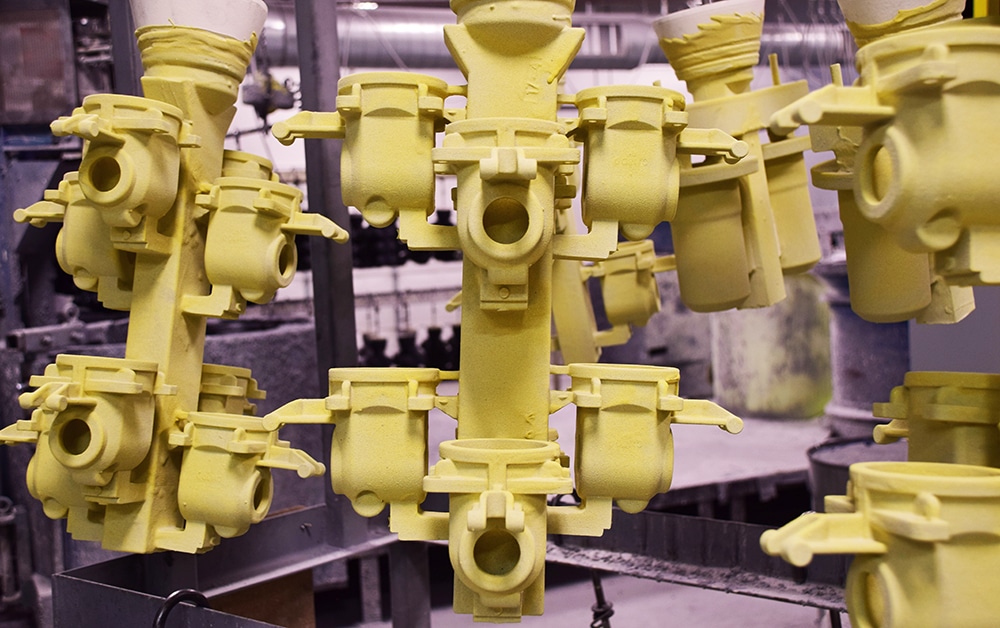
Investment Casting Disadvantages
There are some disadvantages in investment casting, all these points are critical to consider in actual production.
- High tooling and equipment costs: The cost of initial tooling and master pattern is very high. Therefor, it is not justified for low-volume production.
- High technical process: Each step in investment casting requires specific expertise and skilled labor. So any mistake in procedure will result in significant lost for the manufacturers.
- Time-consuming: Several steps in investment casting are time-consuming, like cooling and coating. The total casing process is very slow, it is not suitable for projects with fast lead time.
MIM vs Investment Casting Comparison
Materials Options
Both MIM vs Investment Casting are able to produce strong and durable metal parts with various alloys. Normally, investment casting has a wider variety of metal materials. While MIM is more suitable for alloys with higher melting temperature. Aluminium alloys cannot work efficiently with MIM technology.
ZCMIM Materials
In ZCMIM, we are able to provide custom MIM feedstock, in order to deliver customized mechanical performance and properties for final applications. In addition, custom MIM materials under specific sintering process will ensure the reliable structure of final parts. Our MIM materials include various ferrous and non-ferrous alloys, such as stainless-steel alloys, low alloy steel, copper, titanium alloy, nickel alloy, and specialty alloys like cobalt-chromium(F-75). Please check ZCMIM materials in following picture.
Investment Casting Materials
Investment casting can work well with diverse materials, including both ferrous and no-ferrous materials. The typical investment casting materials including: steel, stainless steel, aluminum alloys, nickel alloys, cobalt alloys, cast iron, copper alloys.
Part Size and Surface Finish
Metal injection molding is the perfect production technology for small metal parts with high volume. Most MIM parts have weight under 200 grams. Otherwise, investment casting has wider part size from 100g to 100 kg, but it is not suitable for high volume production.
MIM can achieve the surface finish of 1 µm, while investment casting usually get surface roughness of 3 µm. MIM parts provide better surface finish than IC parts.
Production Cost
Tooling cost is the major cost for MIM process, however, the lager scale production of millions per year in MIM will reduce the unit price dramatically. Normally, production volume less than 1,000 per year, investment casting is a more economical process. Quantity is the significant parameter, which affects the final production cost. MIM technology is an ‘economy of scale’ technology, ideal for large scale of millions per year.
Design and Applications
MIM technology is suitable for precise metal parts with high strength and wear resistance. It is ideal for medical and industrial equipment with strict regulatory requirement. Furthermore, MIM parts with scalability and heat resistance have widely application in automotive and electronic industry.
Investment casting has complex casting capabilities, this makes it perfect for various industrial applications, especially efficient for industries with high strength and temperature resistance. Such as lightweight medical instruments with streamlined design, part consolidation hardware and vehicles.
When To Apply MIM or Investment Casting
The decision between MIM and Investment casting depends on various basic factors. Regardless of the material to be processed, we also need to consider the parts size, structure complexity, tolerance requirement, production volume. The ideal part for MIM is less than 100 mm with production volume more than 5,000.
Normally, most metal parts under 15 grams are produced by metal injection molding, as MIM technology allow thinner structures with high efficiency of materials and energy. Meanwhile, 90% metal parts above 100 grams are manufactured by investment casting, since the cost of MIM metal powders is too high. Due to accumulation of MIM experience and materials development, MIM technology can produce maximum weight of 250 grams, while investment casting can create maximum weight of 25 kilograms.
Furthermore, MIM has a shorter process of new parts development and production, as it has less molds and prototype before starting production than investment casting. In addition, MIM parts have higher surface finish quality than IC, which eliminates the post-process for surface quality in investment casting.
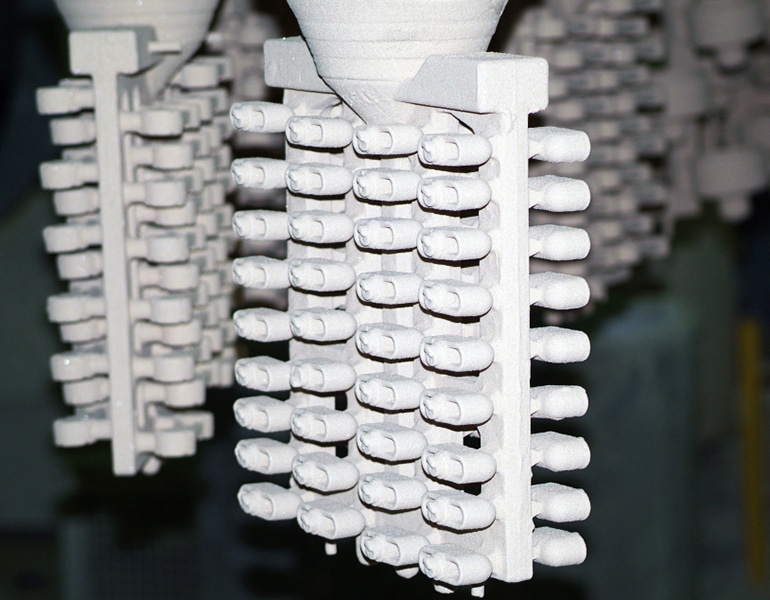
Conclusion
In ZCMIM, we have professional facilities for metal injection molding technology. Our engineering expert team can provide manufacturing simulation of different metal parts, and give technical advice for economical production. We can accompany and support our customers in all manufacturing step, from original design, material selection, manufacturing options to final finishes.