MIM Titanium
Introduction
MIM titanium normally refers to Ti-6Al-4V, it is also known as Ti64, TC4, Titanium Grade 5. It is an alpha-beta titanium alloy with high specific strength and excellent corrosion resistance. The low density and corrosion resistance are necessary for aerospace industry, bio-mechanical applications (implants and prostheses).
Titanium alloys contain the mixture of titanium and other chemical elements. These specific alloys have very high tensile strength and toughness at extreme temperatures. Titanium alloys are light in weight with extraordinary corrosion resistance. However, Ti alloys have high cost in both raw materials and processing. This limits the application in military, aircraft, spacecraft, bicycles, medical devices, premium sport equipment, consumer electronics.
Comparing to conventional stainless steels and cobalt-based alloys, titanium alloys have lower modulus, superior bio-compatibility, and enhanced corrosion resistance. It is the perfect choice as bio-materials. However, Ti64 alloy has poor shear strength and wear resistance, this also restricts the biomedical usages.
Ti-6Al-4V
Common Chemical Composition
MIM Titanium | Ti | Aluminium | Vanadium | iron | Carbon | Nitrogen | Oxygen |
Percent by Weight | Bal. | 5.5.-6.75 | 3.50-4.50 | 0.30 | 0.08 | 0.05 | 0.20 |
Mechanical Properties
Material | Density | Tensile Strength | Yield Strength(0.2%) | Hardness | Elongation(% in 25.4mm) |
MIM Titanium | ≥4.20g/cm³ | ≥750Mpa | ≥650Mpa | 30HRC | ≦10% |
Ti-6Al-4V titanium has two micro-structure phase, alpha (hcp crystal structure) and beta (bcc crystal structure). Aluminum stabilizes the alpha phase, while vanadium stabilizes the beta phase. Ti-6Al-4V has low thermal conductivity, this results in the relatively poor mechinability. In addition, it is vulnerable to cold dwell fatigue.
It has higher strength than commercial pure titanium(grade 1-4), with the same stiffness and thermal properties. This grade is the excellent combination of strength, corrosion resistance, welding and fabricability. The most application titanium is alloyed with aluminium and vanadium of 6% and 4% respectively (Ti-6Al-4V). Ti-6Al-4V is the most common titanium alloy in commercial applications, it takes nearly 70% of total applications.
Titanium MIM
Titanium alloys have high activity, which are prone to react with elements like oxygen, nitrogen and hydrogen. Moreover, micron size metal powder will impact the final physical properties significantly. Titanium metal injection molding (TiMIM) is the perfect method for small implantable medical devices with tight tolerances.
TiMIM technology can produce small and complex titanium parts, including features with tiny grooves, threads, scoring. The common TiMIM medical devices including: pacemaker components, bone repair and replacement components, cataract surgical equipment, ports for catheters, orthodontic brackets. Ti-6Al-4V has excellent bio-compatibility with excellent corrosion resistance, this makes it an ideal candidate.
Regardless the medical devices industry, TiMIM components are also applied in brackets, fasteners, fittings, and other components. There is no doubt that TiMIM is the most manageable and affordable solutions for components with fine feature in the medical and aerospace industry.
Ti-6Al-4V Sintering
Ti-6Al-4V is the most widely applied titanium alloy, it has remarkable mechanical properties for various applications. In addition, it can be tailored for different mechanical properties by mechanical working or heat treatments.
There are two key aspect to control the mechanical properties of MIM Ti6Al4V: micro-structure, final density. In order to achieve adequate density in MIM processing, Ti6Al4V is sintering in temperatures between 1200-1400℃, above the β-transus temperature of 1000℃. This results in the coarse lamellar structure with reduced mechanical properties. Therefore, the key to improve mechanical properties of MIM Ti6Al4V is refining the micro-structure. Fine Ti64 powder, small carbon addition is two key method to achieve micro-structure refinement. Carbon addition can produce Ti6Al4V reinforced with titanium carbides.
Sintering Temperature
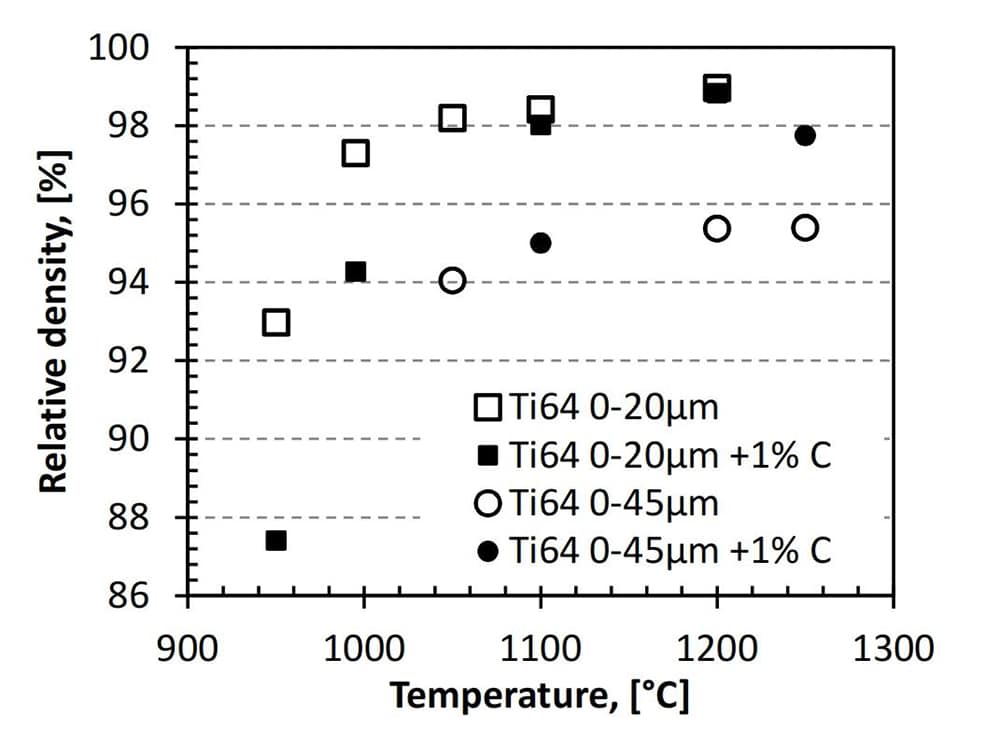
From the graph, above the sintering temperature of 1100℃, all Ti powder can reach at least 95% of theoretical density. Once reach to 1200℃, all Ti powder can achieve the highest density. Above 1200℃, there is no significant change in density. It is obvious that finer Ti powder can start desification process at lower sintering temperature, and achieve higher density at the same sintering temperature.
For 20 µm powder sintering, once sintering temperature above 1100℃, there is the typical micro-structure of MIM Ti6Al4V:
- Relative coarse structure- long acicular α-Ti grains with the thin layer of β-Ti
- Residual pores from incomplete densification
At temperature of 1050℃, the micro-structure start to change, there is no large α-Ti colonies.
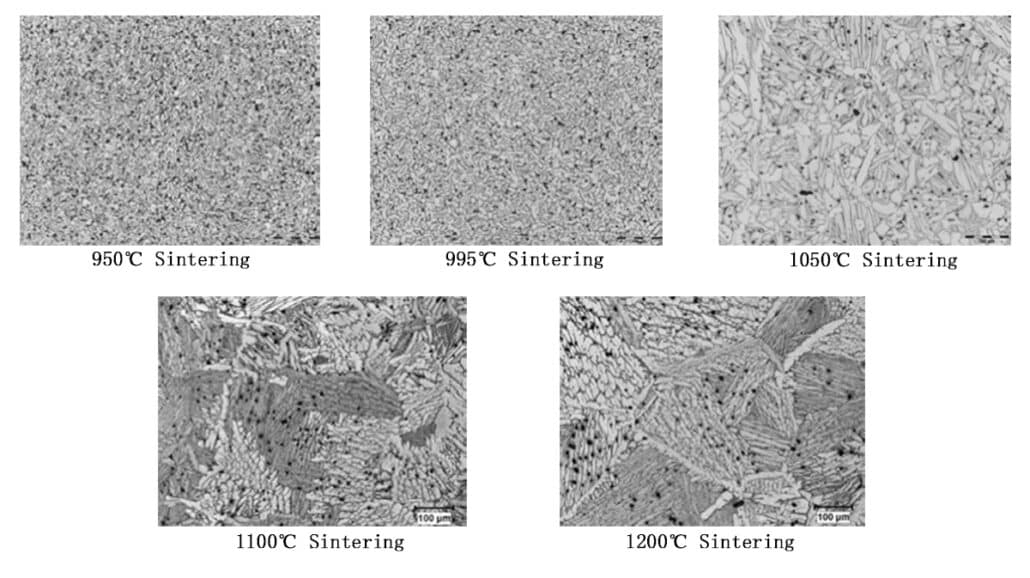
Once sintering temperatures are close to the alpha-beta transition temperatures, nearly 1000℃. The micro-structure become much finer, and α-Ti grains become to more nodular shape. Additionally, the presence of α-Ti grains and lower diffusion kinetics will prevent the excessive growth of the β-Ti grains. All these factors will result in significant change in micro-structure.
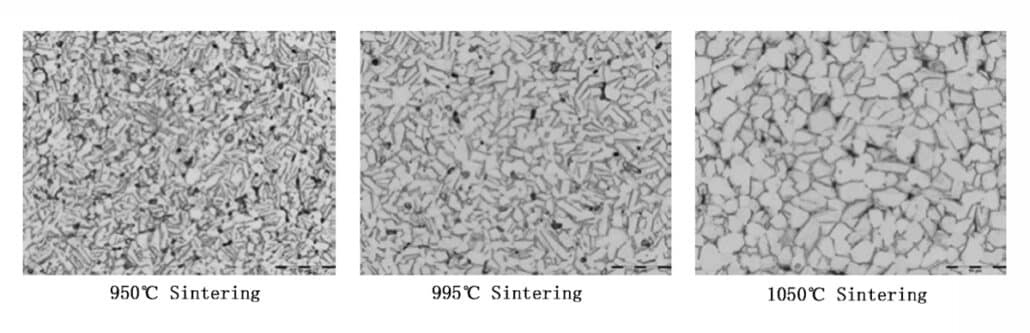
Carbon Additive
Normally, carbon additive will result in more refined micro-structure. This micro-structure is still composed of α-Ti grains with surrounding β-Ti grains, but the α-Ti grains tend to be globular, rather than acicular.
In addition, there are rounded titanium carbide secondary phases in the micro-structure with uniform distribution. These low content of titanium-carbides will impede the growth of β-Ti grains, then refine the microstructure. Titanium carbide can limit the growth of β-Ti grains effectively, event at very high temperature. After 1320℃ sintering, the micro-structure of titanium part has only a fraction of elongated α-Ti grains, and colonies of some α-Ti grains.
The titanium carbide grains have the similar final morphology, whether reaction between carbon particles and titanium matrix, or titanium carbide addition. From the following graph, it is obvious that ,as sintering temperature increase, the titanium carbide will disappear.
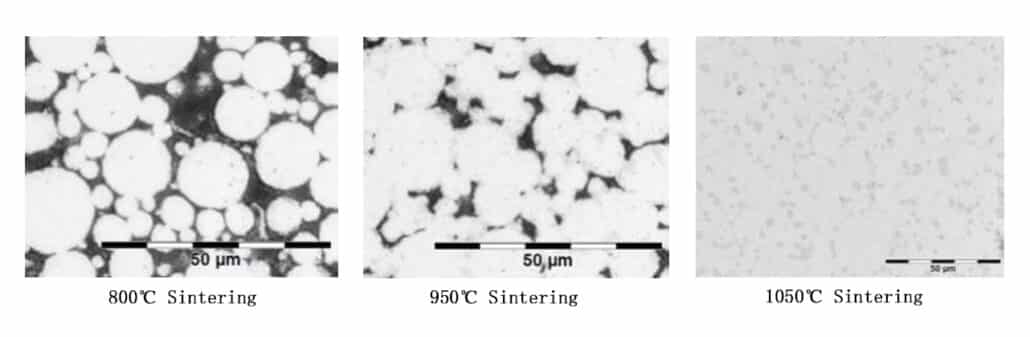
Yttrium Additive
Yttrium element can enhance the the fatigue properties of MIM processed Ti-6Al-4V. There are three factors influence the mechanical properties of Ti-6Al-4V: colony size, porosity, oxygen content. Yttrium oxide is a strong colony refining agent, only 0.1 wt.% of Y2O3 can reduce the colony size of MIM Ti64 from 130µm to 50µm.
Mechanical property, porosity and impurity content in TiMIM process
Ti Composition | YS(MPa) | UTS(MPa) | Elongation(%) | Porosity(%) | Oxygen content (μg/g) | Nitrogen content (μg/g) | |
Initial Powder | 1600 | 2000 | |||||
Ti-6Al-4V | 770 | 880 | 15.3 | 3.5 | 2360±70 | 500±100 | |
Ti-6Al-4V | 0.2% Y | 740 | 850 | 13.2 | 4.3 | 2380±70 | 540±20 |
0.5% Y | 690 | 800 | 12.5 | 5.0 | 2500±95 | 590±70 |
From the above graph, after 1400℃ sintering. The MIM parts of pure Ti-6Al-4V have the yield strength (YS) of 771 MPa, ultimate tensile strength (UTS) of 884 MPa, elongation of 15.3%. However, the addition of yttrium results in the decease of UTS, YS and Elongation. These decrease in strength are caused by porosity increase and reduced oxygen content in the titanium matrix.
In fatigue testing, for pure Ti64, the fatigue strength at 107 cycles is 450 MPa. While the addition of 0.5 wt.% yttrium will increase fatigue strength to 470 MPa at 107 cycles. Therefore, the colony size have more influence on the fatigue behavior than the porosity or oxygen content.
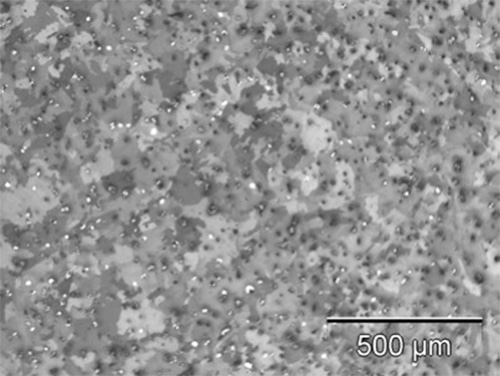
Heat-treatment of Ti64
The heat-treatment of Ti-6Al-4V will vary the amount of micro-structure phase (alpha, beta) in alloy. The common heat-treatment processes are mill annealing, duplex annealing, solution treating&aging. The phase compositions, size, and distributions in Ti64 can be manipulated within certain limitation by heat treatment, in order to permit custom properties.
- Heat treatment can change the large micro-structure below or above the alpha-beta transition temperature, in order to achieve high hardness.
- Solution treatment and aging will produce the maximum strength. Solution aging can cause small β-phase particles to form and strain the crystal lattice. Once aging is performed properly, the additional lattice strain will make alloy tougher, and less to crack.
- Stress-relief heat treatments are also practiced.
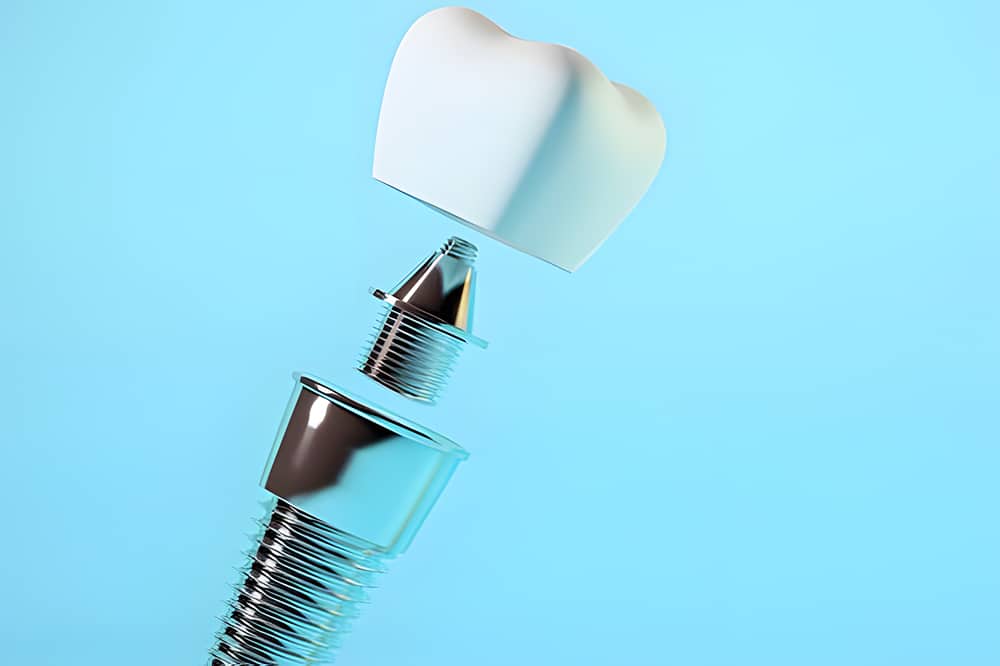
Conclusion
ZCMIM has nearly 10 experience in MIM tatinium. We apply different alloy power size, sintering temperatures, heat treatment to achieve specific mechanical properties. Contact us for your next TiMIM project.