MIM Parts Size Analysis
Introduction
Once, determine whether your parts are fit for metal injection molding process. Part size is the first critical factors. As the most frequent question, “How large parts can you create by MIM technology?”. The quick answer in most case is under 200 grams. However, in our professional design and evaluation process, it is important to realize the parts size impact final MIM cost and efficiency.
Mold Restriction
Part size will never be limited by MIM process, but from the mold size capacity. Normally, the molds has stationary size, once parts size are larger, the fewer parts numbers will be taken up in molds. We can consider molds or tools as one sheet of paper, which has accurate size. When we inject molten MIM materials for required geometry, larger size will fit fewer cavities than small size. This means that, we can add 10 to 20 cavities in one sheet, while only 4 for large size design. For final production quantity of 10,000, smaller size is more production efficient than large size.
Part Complexity
The level of component complexity will dictate which manufacturing process is the best suitable for mass production, in order to guarantee production efficiency. While our normal capacity is less or equal to 200 grams, if parts are too large and complex with typical machining requirement. Metal injection molding process is the most economical way. In order to truly utilize MIM process, Design for Manufacturing (DFM) is the best practice guideline to follow. We should ensure final MIM parts never require expensive secondary operation, or just simple process in final sintering process. This will reduce most of component cost, in addition with less cycle time.
Check our MIM design guideline for MIM designing.
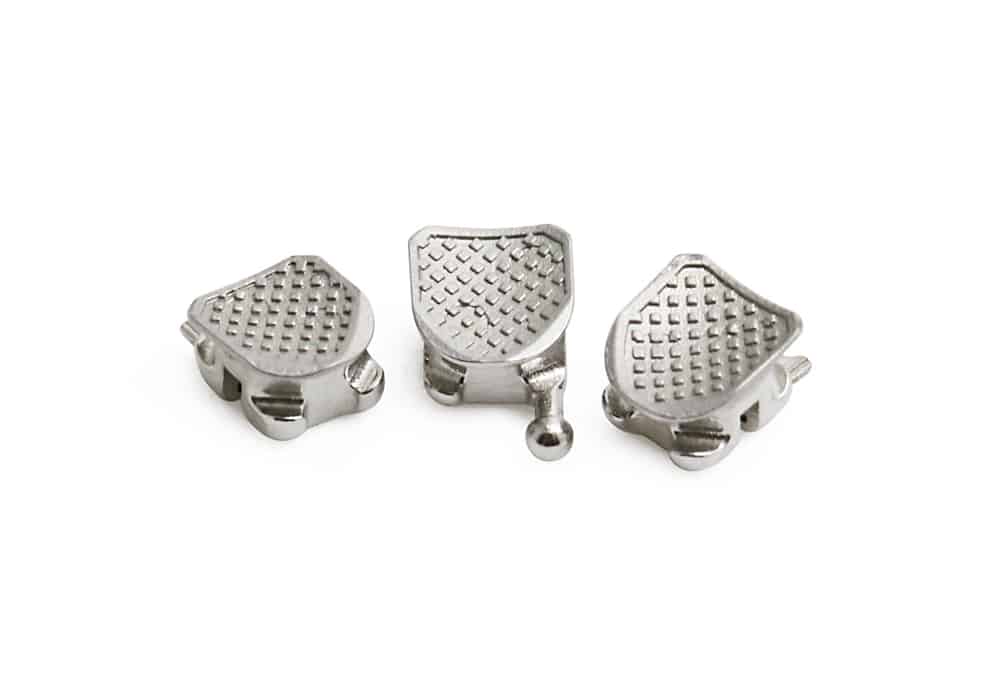
Efficiency with MIM Materials
MIM material is inherent more expensive than average metal material. It is custom with special property requirement. There is no doubt that MIM material cost play an important role in MIM manufacturing process, less material usage determine less cost. In ZCMIM, we optimize our MIM parts design with minimized weight requirement, in addition with no negative effect on parts performance. In this case, we only utilize as little material as possible to create the final component structure. With MIM process, you can add any complexity on MIM parts without any additional material. However, traditional metalworking process like machining or die casting will result in lots of scrap and waste. In some cases, we need to consider the production possibility of traditional technology in complex structure design.
ZCMIM are able to produce any required parts for our customers. Once your designing parts are larger than 200 grams with complex structure requirement. In consideration of economic and production capability, ZCMIM will evaluate our MIM technology to provide the most cost-effective alternative.
Since Metal Injection Molding is capable of achieving intricate features, it improves final MIM geometries design freedom. You can add functional features like dovetails, slots, undercuts, fins, internal and external threads, or curved surface to your design. In reason of MIM utilize injection forming technology, it can produce unique cylindrical structure with greater length to diameter ratio than other traditional casting technology.
Learn more about our MIM capability, contact us to discuss your project requirement now.
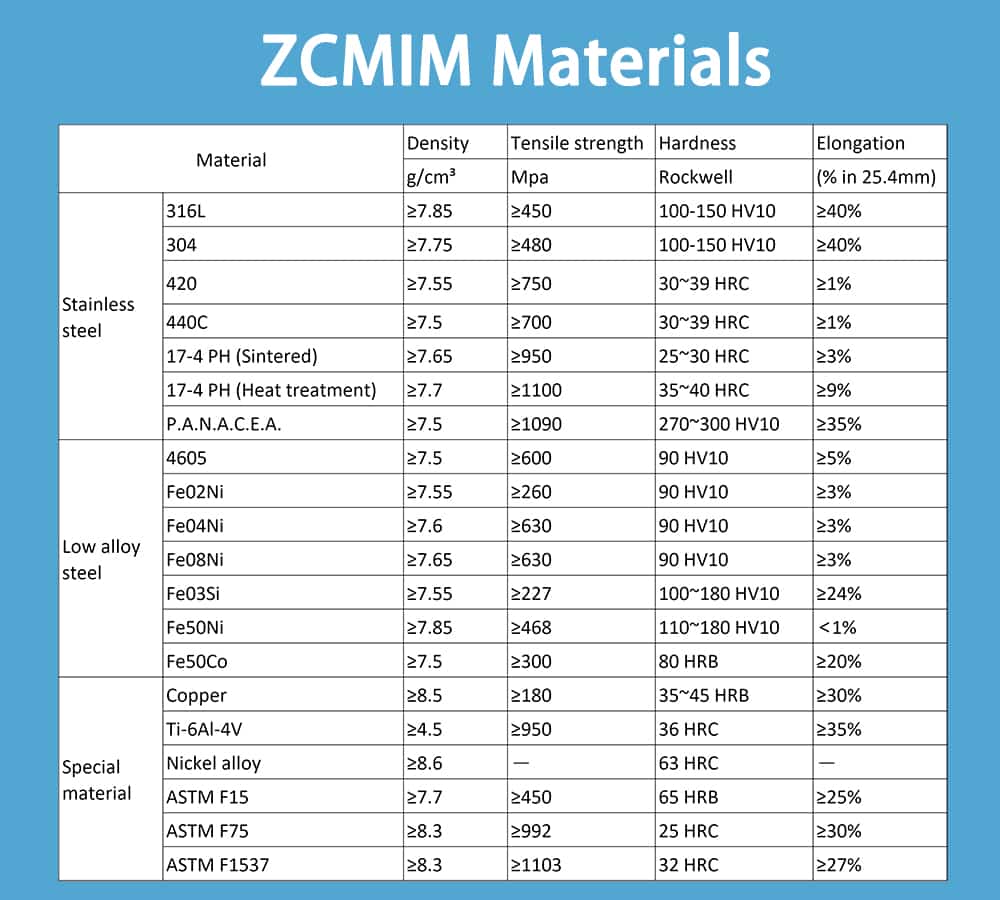
Debinding and Sintering
In MIM manufacturing process, molding, debinding and sintering have strict operation guidelines, which regarding mass loading for each batch size. In order to remove binder material at proper and precise rate. For larger and thicker parts, it will need more furnace space and time to debind and sinter. Once consider of process cycle cost and time, this means more cost in final parts production. ZCMIM engineering team has excellent experience in MIM design and production process, we will modify your design to reduce final parts production time. Thin wall and minimized MIM material usage will optimize your parts for MIM process.
MIM provides a cost-effective solution for small complex component. However, in specific case, it also needs expensive secondary operation by other metal-working method. With MIM technology advantages, ZCMIM supply widely application in various industries, including electronic, medical, automotive and other industrial tools.
Free MIM Design
In traditional metalworking process, design limitation is a critical issue in designing process. Consider of practical manufacturing process and actual producing machine, all these limitations always affect final part physical and chemical performance. In MIM design, engineers are able to have more freedom to create parts geometries. They can utilize material effectively for function and strength requirement. Furthermore, eliminate unnecessary post-operation. MIM technology encourage metalworking in a high level of complex shape with less material usage.
Design for Manufacturing
Sintering support
Draft– location and duration
Fillets and Radii
Ribs and Webs
Gating– types and location
Sink– sink and kit line
Wall thickness
Parting line
Design of Part Improvement
Coring holes
Holes and slots
Undercuts–external and internal
Threads
Decorative features– knurling, lettering, logos
Thickness transition
In order to fully utilize MIM technology, connect with our engineering team to discuss your part design. Our experienced team will professional suggestion on optimal MIM design.
Cost-effective Solution
MIM provides lower cost solutions for numerous industrial applications comparing to traditional metalworking technologies. Although parts size is not the necessary driving factor, it is definite most critical factor of consideration. Once you need small, complex part with higher strength requirement in large volume production, your project will be well benefit from design freedom and cost-effective solution of MIM process.
If you are interested in MIM process, contact our professional engineering team. We will cooperate with you through the whole MIM manufacturing process, and recommend all benefits specific to your unique project.