MIM Copper
Introduction
Copper MIM and its alloys have excellent thermal and electrical conductivity, these properties are suitable for application in electrical and electronic industry. The main products in copper MIM are connectors, switches, heat sinks. All these MIM parts are essential in efficient heat dissipation or reliable electrical connection.
Common Chemical Composition
MIM Copper | Copper | Carbon | Oxygen | Iron | Nickel | Zinc | Stannum |
Percent by Weight | Bal. | 0.00-0.02 | 0.00-0.10 | 0.05 |
Mechanical properties (Sintered)
Material | Density | Tensile Strength | Yield Strength(0.2%) | Hardness | Elongation(% in 25.4mm) | Thermal Conductivity |
MIM Copper | ≥8.50g/cm³ | ≥180Mpa | ≥60Mpa | 35-45 HRB | ≥30% | 330W/mK |
CuMIM
Copper is a soft, malleable and ductile metal with very high thermal and electrical conductivity. The copper alloys including:
- Brass: copper and zinc alloy
- Bronze: copper-tin alloy
- Cupronnickel: copper and nickel alloy
- Tungsten-Copper: copper and tungsten alloy
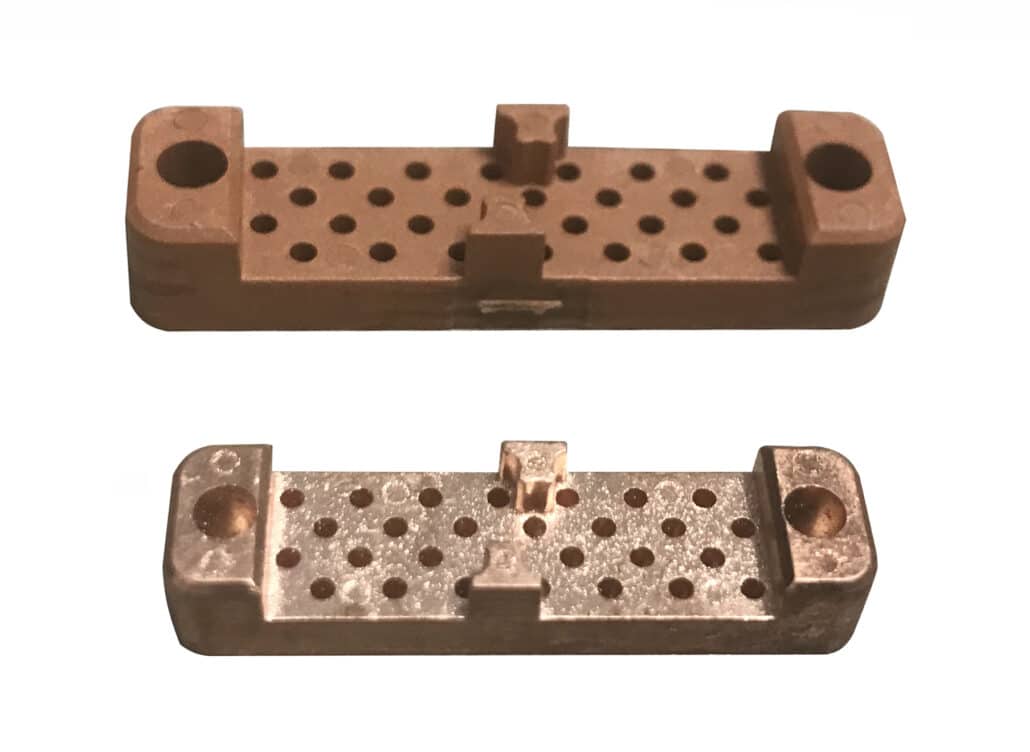
Properties and Characteristics of Copper Alloys
- Excellent electrical and thermal conductivity
- Relative softness and ductility
- Low melting point than steel and titanium alloys
- Susceptible to corrosion and tarnishing
- Copper-zinc alloy(brass) or Copper-tin alloy (bronze) have increase strength
- Tungsten-copper alloys have high tarnish&corrosion resistance
- Common alloy densities around 8.5-9.0 kg/L
Main Application in Copper MIM
- Molding electrical contacts and connectors
- Braking components and friction disks with high wear resistance
- Heat sinks and exchanges with leveraging thermal conductivity
- Gears or cams with low-force transmission
- Decorative parts in jewelry and fittings
Copper MIM alloys have excellent conductivity and flexibility, these alloys are suitable for electrical, thermal, and moderate load-bearing applications. In addition, custom properties can achieve with alloying additions.
Copper Metal Injection Molding
Copper MIM (Copper Metal Injection Molding, CuMIM) is an advanced fabrication technology for high-complex copper parts with reduced cost. Due to the exceptional thermal and electrical conductivity of copper, CuMIM can produce intricate structure of copper parts in electronic and automotive industries.
We applies CuMIM technology to manufacture unconventional copper heat sink for electronic, automotive and optoelectonic applications. These copper parts are designed with different structure and complex geometry, in order to mount on different area for heat dissipation.
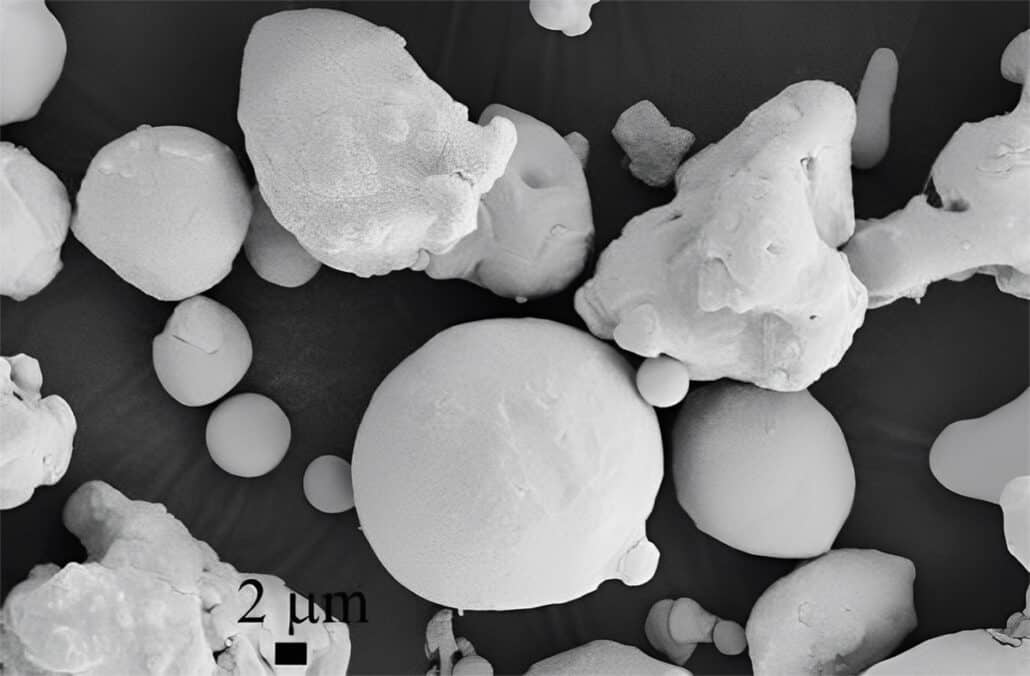
ZCMIM can apply pure copper in MIM technology, we can design unconventional geometry for electronic, automotive and optical-electronic applications. CuMIM with pure copper material, can produce components with 320 W/mK thermal conductivity. There copper parts also can be designed with complex geometry.
Benefits of Copper MIM
- Copper MIM is crucial for maintaining electronic device performance by effectively dissipating heat.
- CuMIM can manufacture complex geometries with high performance.
- Copper MIM is economical and effective for small size, complex shape Cu products.
- Power performance is the key factor affecting the MIM process.
- The superior heat dissipation properties also contribute to efficient system operation in automotive sectors.
Bronze MIM (CuSn MIM)
Bronze is a copper alloy with 12-12.5% tin, other metals (aluminium, manganese, nickel, zinc) or non-metals(phosphorus, arsenic, silicon). this kind of alloys are harder than pure copper, and have useful properties like strength, ductility, or machinability.
Bronze Properties
Bronze alloys have lower melting point than steel, but 10% higher density than steel. Bronze has high heat and electric conductivity than most steels. The cost of bronze alloys are higher than steels, but lower than nickel-base alloys. In addition, bronzes are typically ductile alloys, and less brittle than cast iron.
- Pure copper: High electrical conductivity
- Bearing bronze (high lead content 6-8%): low-friction properties
- Bell bronze(20% tin, 80% copper): corrosion resistance to sea water
Bronze parts are typically tough, the common applications are bearings, clips, electrical connectors and springs, bushings, automobile transmission pilot bearings, bearings of small electric motors.
Brass MIM (CuZn MIM)
Brass is an alloy of copper and zinc, different proportions will achieve different properties in color, mechanical, electrical, acoustic, and chemical. Brass alloys also contain small proportions of arsenic (As), lead (Pb), phosphorus (P), aluminium (Al), manganese (Mn), and silicon (Si).
Brass Properties
Brass has low melting point, high workability, durability, electrical and thermal conductivity. High copper content brasses are softer and more golden color, conversely brasses with low copper content are harder and more silvery color. By varying the proportions of copper and zinc, brass properties are altered into hard and soft.
Brass has high malleability than bronze or zinc, and low melting points (900℃ to 940℃ on different composition). Its flow characteristics make it a easy material in casting process. The common density of brass is 8.4 to 8.73 kg/L.
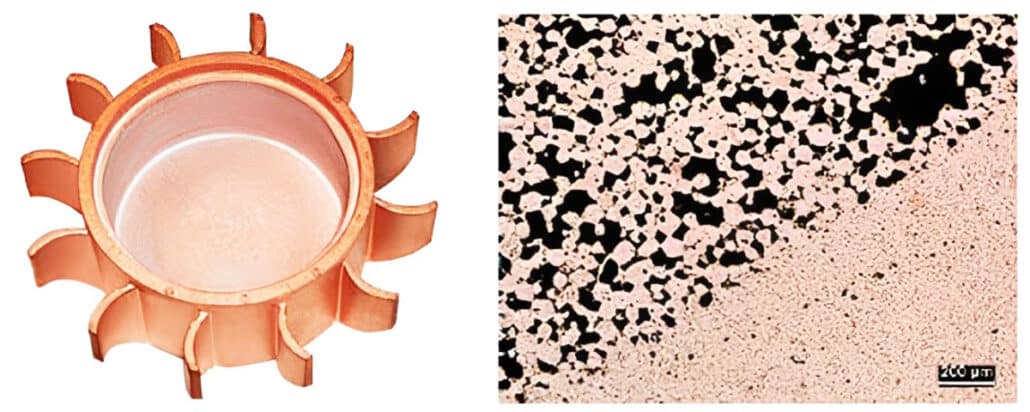
Brass Additives
Aluminium(Al)
Aluminium increases brass strength and corrosion-resistance, it can form a highly beneficial hard layer of aluminium oxide(Al2O3), this layer is thin, transparent, and self-healing.
Tin (Stannum)
Tin has similar effect as aluminium, especially in seawater applications like naval brasses.
Iron(Fe)
1% addition of iron to brass alloy will create the alloy with noticeable magnetic attraction.
Lead(Pb)
Lead is a common additive to enhance the machinability of brass, the normal concentration is about 2%.
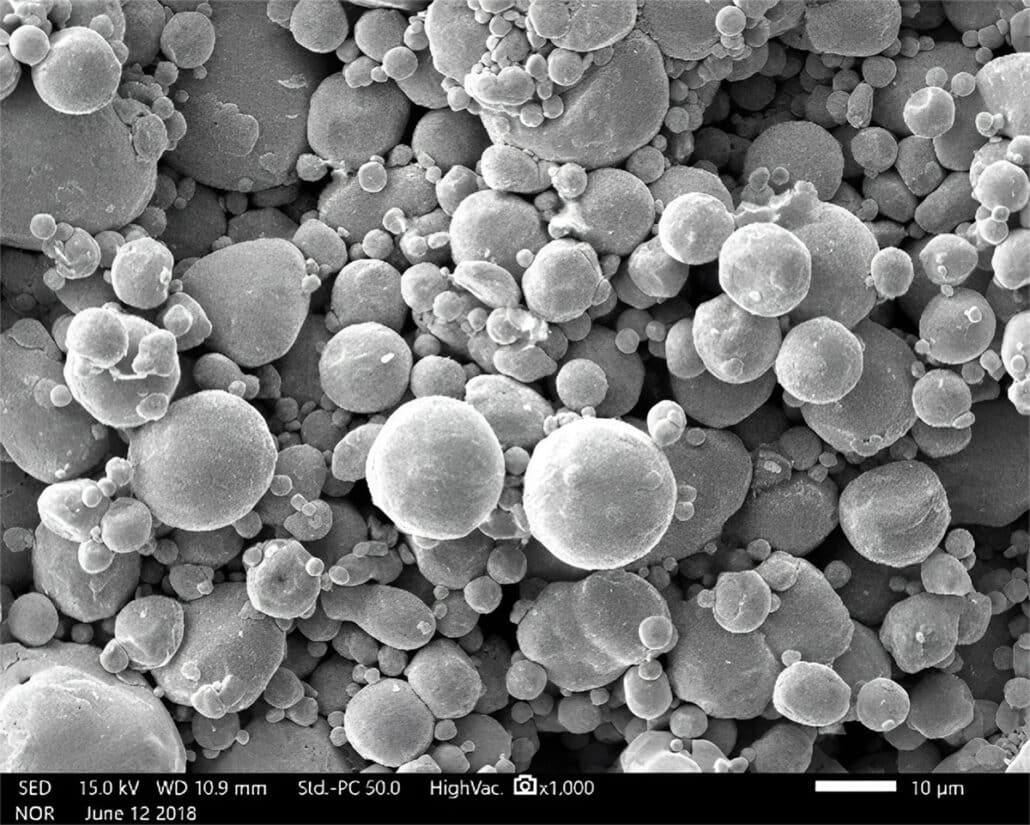
Copper-Tungsten MIM
Copper-tungsten is also know as tungsten-copper, CuW, or WCu. It is a mixture of copper and tungsten. Since copper and tungsten are not mutually soluble, the CuW material is distinct particles dispersing of one metal in a matrix of the other one. Therefore, the micro-structure of CuW is rather a metal matrix composite, instead of a true alloy. Commonly, the copper-tungsten mixtures contains 10-50 wt.% of copper, the remaining portion are mostly tungsten.
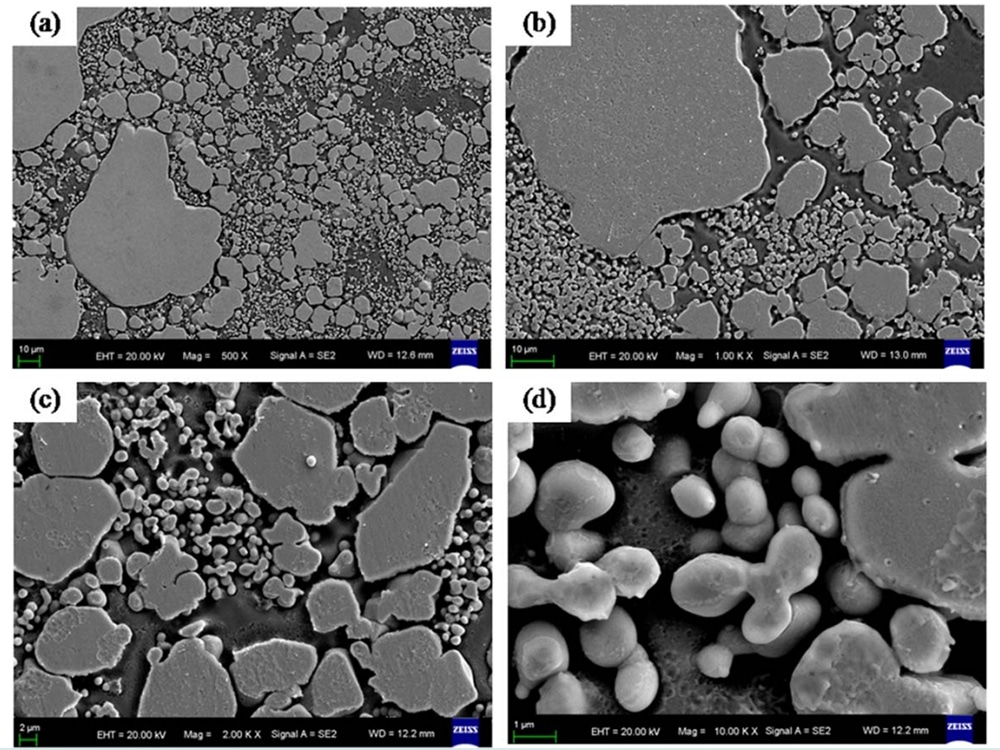
Tungsten Copper MIM is a new type of powder forming technology, feedstock with W-Cu mixed powder are molded into required structure, then debound and sintered to net-metal parts.
CuW Properties
The CuW materials combine the properties of both metals, including: heat-resistance, ablation-resistance, highly thermal and electrical conductivity, easy machining.
Tungsten-copper alloys have distinctive properties of low coefficient of thermal expansion(CTE). this kind of alloys are essential for compact systems with minimizing thermal expansion. This will eliminate the challenges of high CTE of pure copper parts. For low CTE applications, tungsten-copper alloys are ideal to over this challenge. Tungsten has favorable CTE, it can effectively mitigate copper expansion by heat. We can design the custom degree of expansion by adjusting the ratio of tungsten to copper in the alloy, in order to satisfy specific requirements. The higher tungsten proportion results in less expansion, while higher copper leads to higher expansion.
CuW Applications
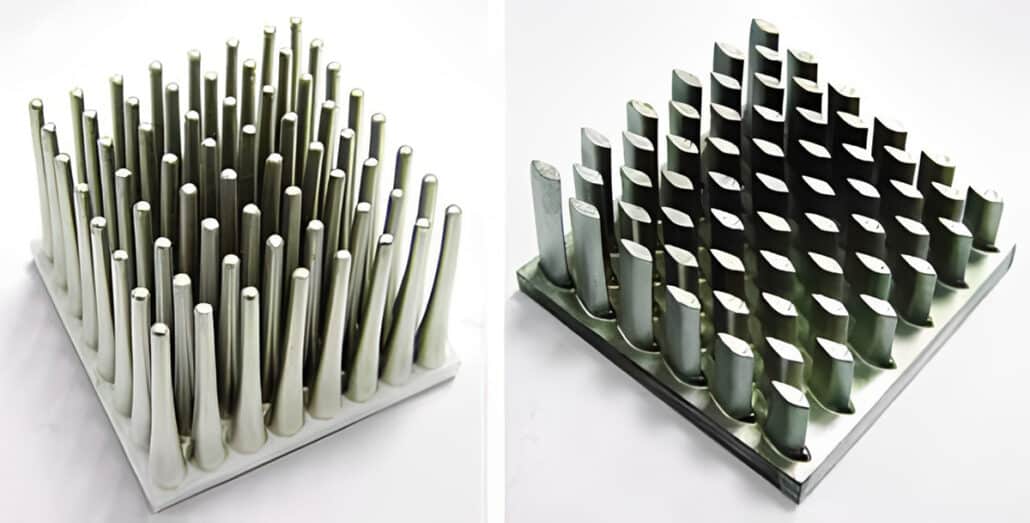
CuW composites are applied in situation with requirement of heat resistance, high electrical and thermal conductivity, and low thermal expansion. Including electrical contacts, heat sinks. In addition, CuW is also applied as contact material in vacuum, it is good choice for vacuum contact since its low cost, arc erosion resistance, mechanical wear and contact welding resistance.
CuW75 is applied widely for power semiconductor devices in chip carriers, flanges, substrates, and frames. W-15Cu,W-20Cu is the common composition for heat sink.
Conclusion
ZCMIM has nearly 10 experience in MIM copper. We apply different alloy power size, alloy proportion, heat treatment to achieve specific electronic and mechanical properties. Contact us for your next Copper MIM project.