Micro Metal Injection Molding
Micro metal injection molding (Micro MIM) is an advanced technique of metal injection molding (MIM), it applies sub-μm size metal powders and micro-size mold to produce tiny parts. Comparing to the conventional MIM products, the dimension accuracy is within tenth of micrometers. Micro MIM can ensure dimensional accuracy within a few micrometers. However, it is difficult to achieve in practical productions.
μ-MIM has capability of tiny metallic parts with micro-size and microstructure. The micro-miniaturization in Micro MIM is challenging with various technical issues of dimension and structure. Such as incomplete filling of narrow cavity in injection molding, demolding failure of fragile green parts, structure deformation in debinding and sintering process. Therefore, Micro MIM (μ-MIM) is a sophisticated manufacturing technology for tiny metal parts with microstructure.
Micro MIM Powder
Gas Atomized Metal Powder
Gas atomized metal powder is designed specially for micro-metal injection molding (micro – MIM), this metal powder has finer size than water atomized powder. It also has spherical structure, this will increase mold filling efficiency.
The common micro MIM powder including:
- Master alloys
- Cobalt alloy
- Nickel alloy
- Stainless steel
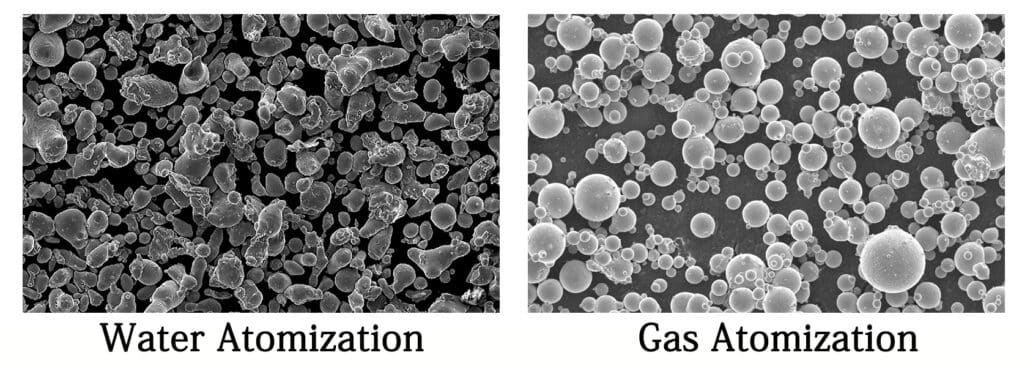
Master Alloy
In micro MIM, master alloy powders can be blended with carbonyl iron powder with precise design. In order to achieve the chemical composition of pre-alloy equivalent in the final sintered components. There are a number of benefits in master alloy technology:
- Low distortion in debinding and sintering process.
- Shorter sintering time than pre-alloy metal powders.
- High sintering density.
- Excellent mechanical properties equal to wrought materials
The typical Master Alloy with nominal chemical composition
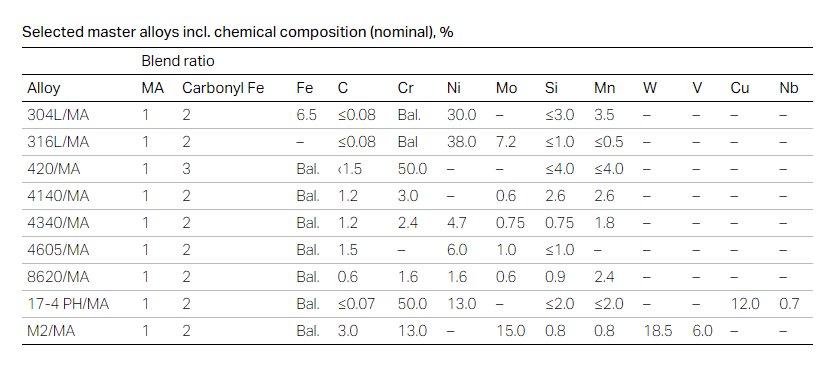
Metal Powder Characteristics
Gas atomized metal powder for Micro MIM has the spherical morphology, it results in high packing density of metal powders. Therefore, it enables the production of MIM feedstock with high powder loading. This specific feedstock will minimize binder cost, and reduce shrinkage in debinding and sintering process. Furthermore, high spherical metal powder has excellent flow characteristics, this increases the consistent mold filling in micro MIM injection molding.
The low oxygen content of Micro-MIM powder will ensure better control of carbon in sintering process. In addition, low oxygen and high packing density will also facilitate faster sintering.
Particle Size Distributions
Metal powder for Micro MIM (μ-MIM) has the typical particle size distribution as following:
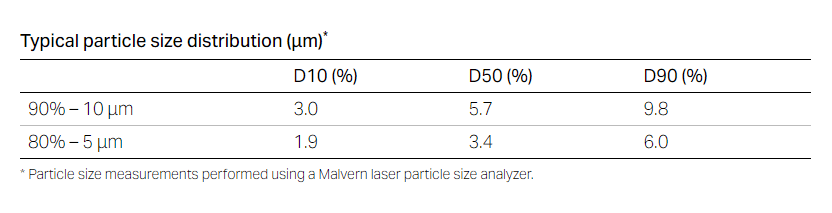
Otherwise, depending on different type of alloys and vendors, there are still different particle size distributions. Please check the particle size distribution and date sheet from Sandvik Ospery:
Micro MIM Benefits
Micro-MIM is a variant of metal injection molding, it is applied for tiny parts production. Naturally, μ-MIM requires exceptionally fine powder to create precise geometries and surface finishes. Micro-MIM provides several major benefits over conventional MIM process:
- Micro MIM can manufacture intricate feature, such as undercuts, threads and slots.
- μ-MIM produces higher density and strength than MIM.
- Micro MIM provides smoother surface finishes and higher dimensional accuracy.
- μ-MIM allows ultra-thin wall structure in designing.
Micro MIM Challenges
Because of the micro-size and micro-structure of metallic parts, there are more technical challenges in each μ-MIM process.
- It is difficult to inject feedstock completely into the narrow cavity. Therefore, we require more methods to increase the injection efficiency. For examples: increase injection pressure, mold design adjustment.
- It is critical to demold fragile green compacts from the metallic mold. Multiple ejection pin are applied to improve total ejection forces, while decrease ejection force on single points, alternative parting-line to improve.
- Support plates are a key element to avoid any slight deformation in debinding and sintering process.
Micro MIM vs Conventional MIM
As Micro MIM technology applies more fine metal powder than conventional MIM. It is suitable for components with size and tolerance requirements, which are difficult to achieve by conventional MIM technology. We summarize the nominal accuracy between Micro MIM and Conventional MIM in the following table:
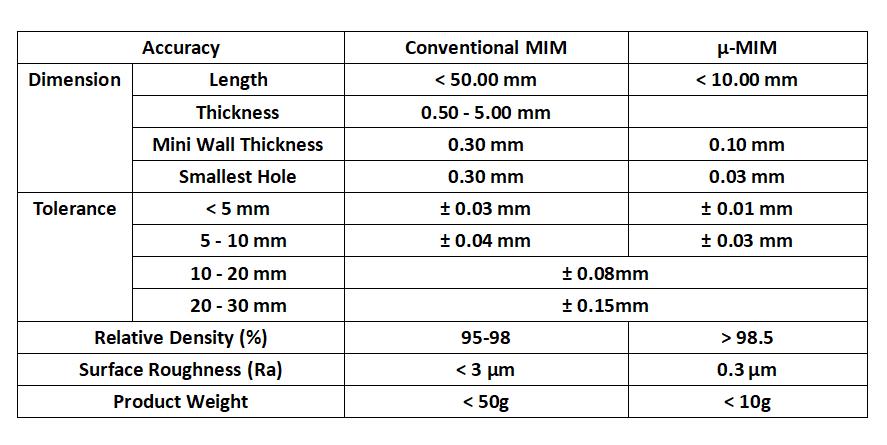
Micro MIM Application
Micro MIM is invaluable for component miniaturization in various application, specific in micro electrical-mechanical systems (micro gears, micro motors), micro fluidic devices and micro medical devices.
Micro Gear
Micro MIM is able to produce micro gear with high accuracy, it can replace traditional technologies like die casting, hobbing, milling and powder metallurgy (PM). The micro gears have widely applications in small gear box, robot toys, mobile phone camera.
The molds in micro gears are usually three-plate molds. In addition, the mold structure for helical gear is much more complicated, it also requires specific ejection mechanism. The ejection speed is controlled precisely and appropriately during commissioning. In order to avoid any defects on green products.
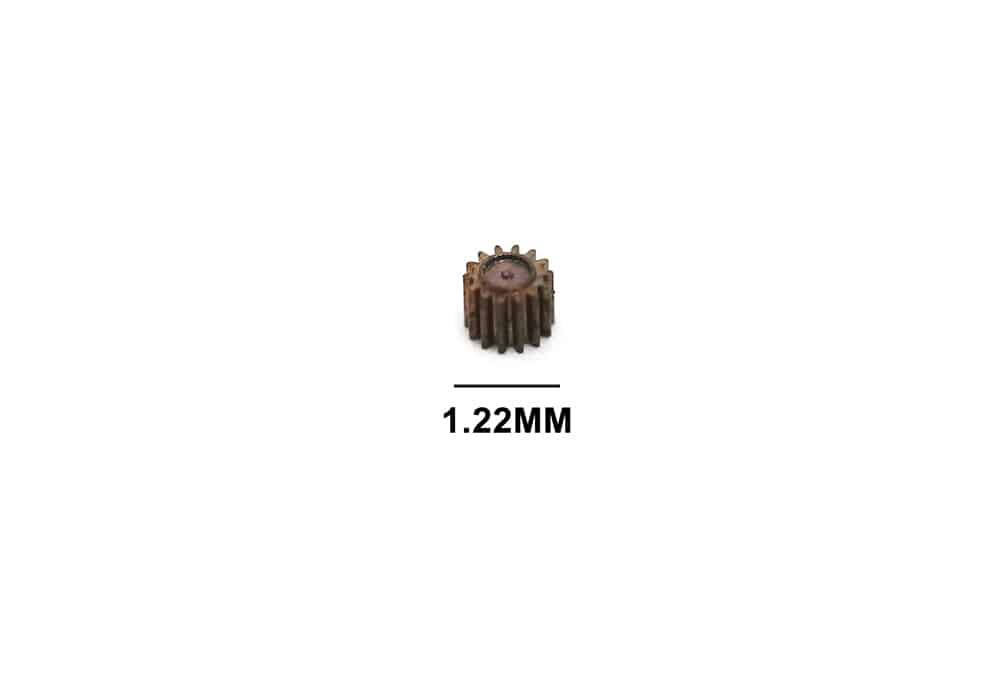
Micro Medical Devices
In ZCMIM, we can apply micro MIM technology to produce micro medical part with complex geometry, such as teeth orthodontic bracket in the following picture. In this micro-mechanical component, there are many complex features, which are only can be seen under the microscope. Therefore, our engineering team develop a specific tooling design, in order to ensure the smooth injection molding without any defects in each cavity.
Furthermore, we also apply an additional optical measuring process to check the final sintered parts, this will guarantee the high quality of complex structure in micro MIM parts.
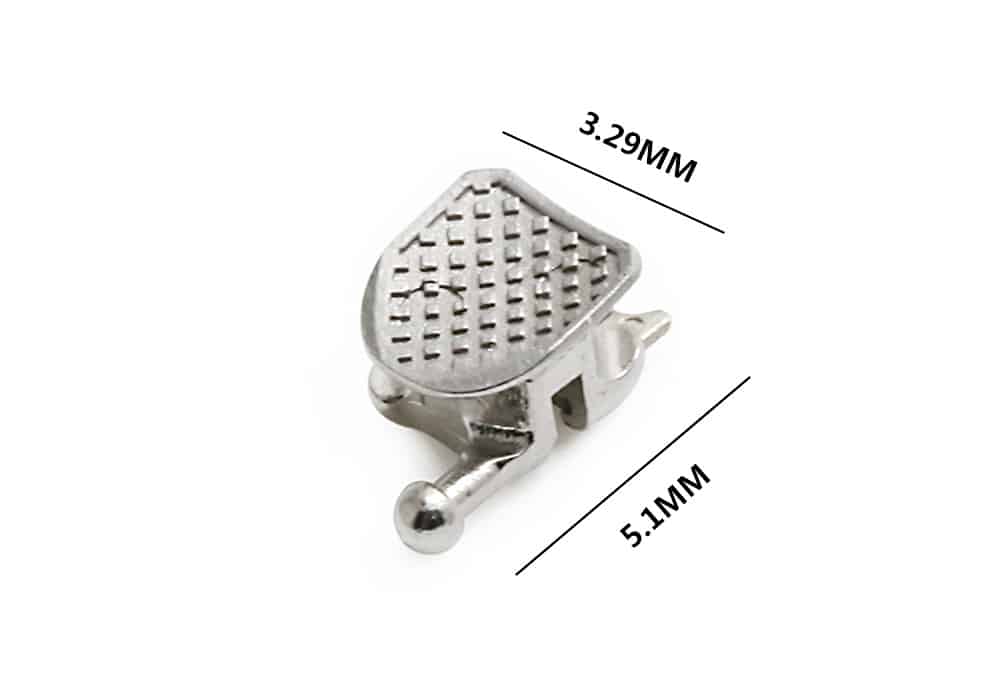
Conclusion
In ZCMIM, our professional engineering team has abundant experience in both Micro MIM and Conventional MIM. We are able to produce various micro metal components for different industry.